直縫鋼管管道防腐的辦法
Anti-corrosion Measures for Straight Seam Steel Pipeline
外壁防腐涂層:管道外壁涂層資料品種和運(yùn)用條件。
Anti-corrosive coatings on the outer wall of pipelines: materials and operating conditions of coatings on the outer wall of pipelines.
內(nèi)壁防腐涂層:爲(wèi)了避免管內(nèi)腐蝕、降低摩擦阻力、進(jìn)步輸量而涂于管子內(nèi)壁的薄膜。常用的涂料有胺固化環(huán)氧樹脂和聚酰胺環(huán)氧樹脂,涂層厚度爲(wèi) 0.038~0.2毫米。爲(wèi)保證涂層與管壁粘結(jié)結(jié)實(shí),必需對管內(nèi)壁停止外表處置。70年代以來趨向于管內(nèi)、外壁涂層選用相反的資料,以便管內(nèi)、外壁的涂敷同時(shí)停止。
Inner wall anticorrosive coating: To avoid corrosion in the pipe, reduce friction resistance, improve the flow rate and coat the film on the inner wall of the pipe. The common coatings are amine cured epoxy resin and polyamide epoxy resin. The thickness of coatings is 0.038-0.2mm. In order to ensure the bonding between the coating and the pipe wall, it is necessary to stop the external disposal of the pipe wall. Since the 1970s, it has tended to choose the opposite material for inner and outer wall coatings, so that both inner and outer wall coatings can be stopped at the same time.
防腐保溫涂層:在中、小口徑的熱輸原油或燃料油的管道上,爲(wèi)了增加管道向土壤散熱,在管道內(nèi)部加上保平和防腐的復(fù)合層。常用的保溫資料是硬質(zhì)聚氨脂泡沫塑料,適用溫度爲(wèi)-185~95℃。這種資料質(zhì)地堅(jiān)實(shí),爲(wèi)進(jìn)步其強(qiáng)度,在隔熱層里面加敷一層高密度聚乙烯層,構(gòu)成復(fù)合資料構(gòu)造,以避免地下水滲入保溫層內(nèi)。
Anti-corrosion and thermal insulation coating: In order to increase the heat dissipation of pipeline to soil, a compound layer of flatness and anti-corrosion is added to the pipeline on medium and small diameter pipelines for heat transportation of crude oil or fuel oil. The commonly used heat preservation material is rigid polyurethane foam, and the applicable temperature is - 185 - 95 C. In order to improve its strength, a layer of high density polyethylene (HDPE) is added to the thermal insulation layer to form a composite data structure to avoid groundwater infiltrating into the thermal insulation layer.
電法維護(hù)
Electrical maintenance
改動(dòng)金屬于四周介質(zhì)的電極電位,使金屬免受腐蝕的辦法。長輸管道電法維護(hù)僅指陰極維護(hù)和電蝕避免法。
Change the electrode potential of the metal absolutely in the surrounding medium, so that the metal is not corroded. Electrical maintenance of long distance pipeline only refers to cathode maintenance and corrosion avoidance.
陰極維護(hù):將被維護(hù)金屬極化成陰極來避免金屬腐蝕的辦法。這種辦法用于船舶防腐已有 150多年的歷史;1928年一次用于管道,是將金屬腐蝕電池中陰極不受腐蝕而陽極受腐蝕的原理使用于金屬防腐技術(shù)上。應(yīng)用外施電流迫使電解液中被維護(hù)金屬外表全部陰極極化,則腐蝕就不會(huì)發(fā)作。判別管道能否到達(dá)陰極維護(hù)的目標(biāo)有兩項(xiàng)。一是小維護(hù)電位,它是金屬在電解液中陰極極化到腐蝕進(jìn)程中止時(shí)的電位;其值與環(huán)境等要素有關(guān),常用的數(shù)值爲(wèi)- 850毫伏(于銅-硫酸銅參比電極測定,下同)。二是大維護(hù)電位,即被維護(hù)金屬外表允許到達(dá)的高電位值。當(dāng)陰極極化過強(qiáng),管道外表與涂層間會(huì)析出氫氣,而使涂層發(fā)生陰極剝離,所以必需控制匯流點(diǎn)電位在允許范圍內(nèi),以使涂層免遭毀壞。此值與涂層性質(zhì)有關(guān),普通取-1.20-2.0伏間。完成地下管道陰極維護(hù)有外加電流法和犧牲陽極法兩種。
Cathodic Maintenance: Polarization of the maintained metal into a cathode to avoid metal corrosion. This method has been used for anti-corrosion of ships for more than 150 years. It was first used in pipelines in 1928. The principle that the cathode of metal corroded batteries is not corroded while the anode is corroded was applied to metal anti-corrosion technology. If the applied current is applied to force the cathodic polarization of the surface of the maintained metal in the electrolyte, the corrosion will not occur. There are two criteria to determine whether the pipeline can reach the goal of cathode maintenance. The first is the minimum maintenance potential, which is the potential of metal from cathodic polarization in electrolyte to the end of corrosion process. Its value is related to environment and other factors. The commonly used value is - 850 mV (absolutely determined by copper-copper sulfate reference electrode, the same below). The second is the maximum maintenance potential, which is the maximum potential allowed to be reached by the surface of the maintained metal. When the cathodic polarization is too strong, hydrogen will precipitate between the surface of the pipeline and the coating, which will lead to the cathodic stripping of the coating. Therefore, it is necessary to control the potential of the confluence point within the allowable range in order to prevent the coating from being destroyed. This value is related to the properties of the coating. It is usually taken between -1.20 and -2.0 volts. There are two methods for cathode maintenance of underground pipelines, i. e. external current method and sacrificial anode method.
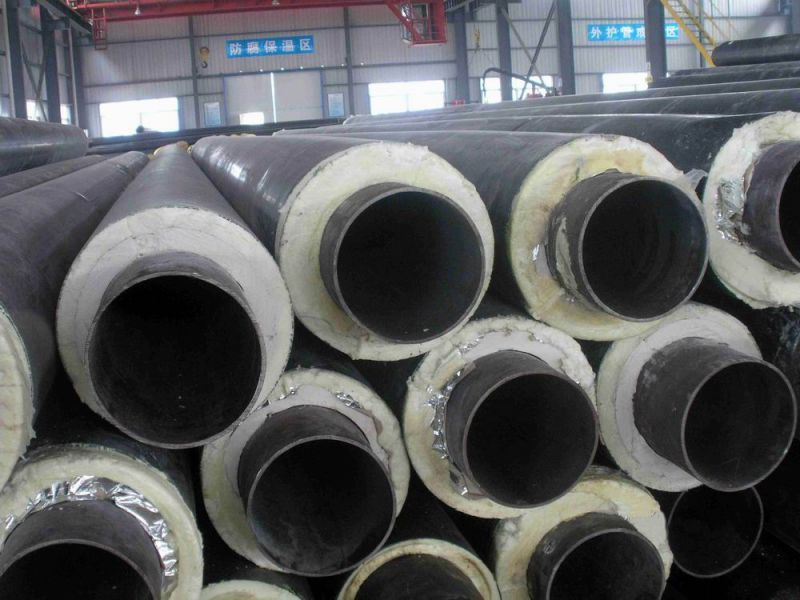
犧牲陽極法是采用比被維護(hù)金屬電極電位更負(fù)的金屬與被維護(hù)金屬銜接,兩者在電解液中構(gòu)成原電池。電位較負(fù)的金屬(如鎂、鋅、鋁及其合金)成爲(wèi)陽極,在輸入電流的進(jìn)程中逐步損耗掉,被維護(hù)的管道金屬成爲(wèi)陰極而免遭腐蝕,所以稱電位較負(fù)的金屬爲(wèi)犧牲陽極。其接線如圖4。 地下管道采用犧牲陽極維護(hù),其決議要素是陽極發(fā)作電流、陽極數(shù)量和維護(hù)長度等。當(dāng)陽種確定后,影響上述參數(shù)的是陽極接地電阻和與該陽極維護(hù)管段區(qū)間的漏泄電阻。前者取決于土壤電阻率,后者取決于管道涂層電阻和涂層的施工質(zhì)量。犧牲陽極運(yùn)用壽命與分量有關(guān),視需求可用幾年幾十年。犧牲陽有投資省、管理簡便、不需求外電源、避免攪擾腐蝕效果好等優(yōu)點(diǎn),所以在地下金屬管道防腐中失掉普遍使用。
The sacrificial anode method is to connect the metal with the maintained metal, which is more negative than the potential of the maintained metal electrode. Both of them constitute the primary battery in the electrolyte. Metals with negative potential (such as magnesium, zinc, aluminium and their alloys) become anodes, which are gradually depleted in the process of input current, and the maintained pipeline metals become cathodes to avoid corrosion, so the metal with negative potential is called sacrificial anode. Its wiring is shown in Figure 4. Underground pipelines are maintained with sacrificial anodes, whose key factors are the current of anode onset, the number of anodes and the length of maintenance. When the type of anode is determined, the above parameters are affected by the grounding resistance of the anode and the leakage resistance of the maintenance section of the anode. The former depends on the soil resistivity, and the latter depends on the resistance of pipeline coating and the construction quality of coating. The service life of sacrificial anode is related to its component, and it can be used for years to decades depending on the demand. Sacrifice anode has the advantages of low investment, simple management, no need for external power supply, good effect of avoiding disturbance and corrosion, so it is widely used in underground metal pipeline corrosion protection.
電蝕避免法:一是在雜散電流源有關(guān)設(shè)備上采取措施,使漏泄電流減小到低限制;二是在敷設(shè)管道時(shí)盡量避開雜散電流地域,或進(jìn)步被攪擾管段絕緣防腐層質(zhì)量,采用屏蔽、加裝絕緣法蘭等措施;三是對攪擾管道作排流維護(hù),行將雜散電流從被攪擾管道排回發(fā)生漏泄電流的電網(wǎng)中,以消弭雜散電流對管道的腐蝕。依據(jù)使用范圍和排流設(shè)備的不異性能,分間接排流、極性排流、強(qiáng)迫排流三種。對交流攪擾電壓的防護(hù),不少國度都制定有技術(shù)規(guī)則,次要是采用平安間隔和管道泄流兩類辦法使管道免遭損害。
Corrosion avoidance method: first, take measures to reduce leakage current to the minimum limit on stray current source related equipment; second, avoid stray current area as far as possible when laying pipelines, or improve the quality of insulating anticorrosive layer of disturbed pipeline section, adopt shielding, installing insulating flange and other measures; third, make drainage maintenance for disturbed pipelines. The stray current will be discharged from the disturbed pipeline back to the leakage current grid to eliminate the corrosion of the stray current to the pipeline. According to the scope of use and the non-uniform performance of drainage equipment, there are three types: indirect drainage, polar drainage and forced drainage. For the protection of AC disturbance voltage, many countries have formulated technical rules. Secondly, safe interval and pipeline discharge are used to protect pipelines from damage.
In summary, all the above-mentioned Shandong Hipper Pipe Technology Development Co., Ltd. provides, want to know more about the black jacket straight-seam steel pipe, welcome to pay attention to our website: http://www.qndr49.cn Thank you for your support!